Aseptic Preparation
Providing expert advice and guidance on aseptic preparation processes to ensure safety and compliance.
Optimising aseptic processes for safety, efficiency, and regulatory compliance
Manufacturing
Facility Design
Supporting layouts, workflows, and start-up plans for new aseptic units
Quality Management
Building QMS frameworks aligned with MHRA and EU GMP requirements
Audit Preparation
Helping teams get inspection-ready with mock audits and compliance walkthroughs.
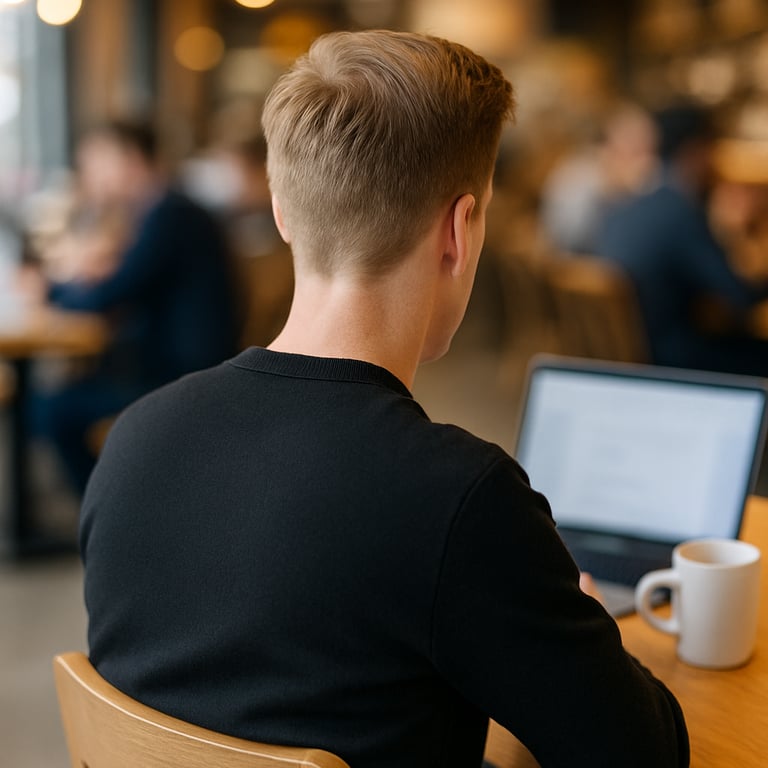
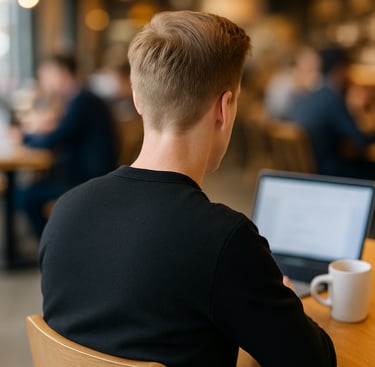
Document Support
Authoring and reviewing SOPs, forms, work instructions, and GMP templates.
Our Services
Creating engaging training content and role-specific competency frameworks.
Training Packages
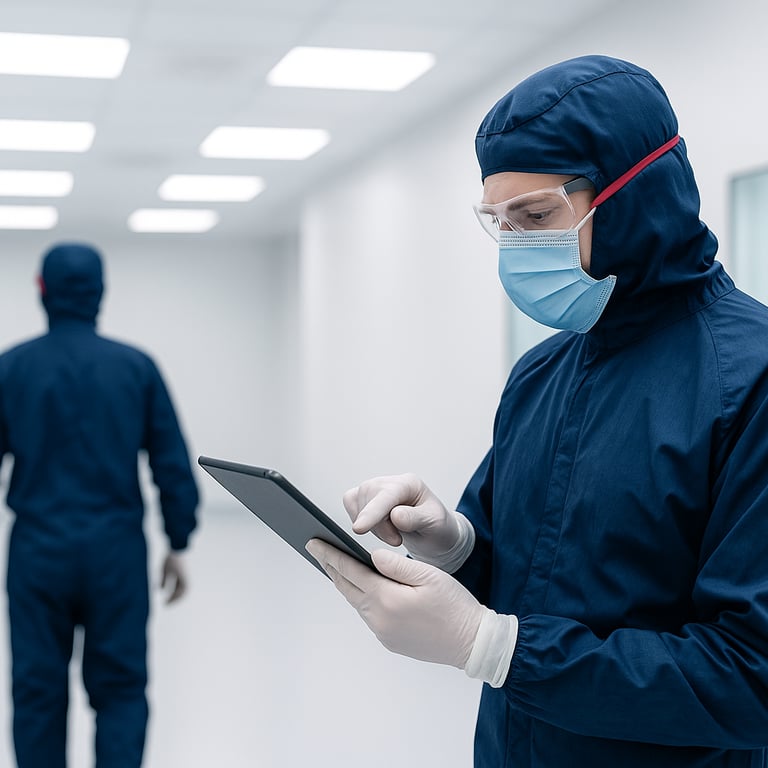
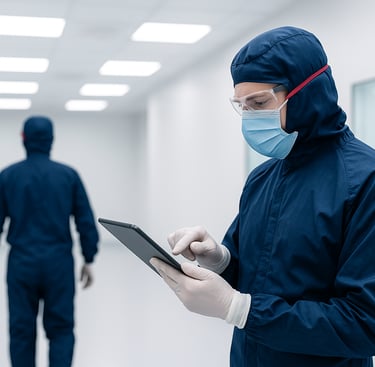
Helping you structure rotas, roles, and operational culture in aseptic services.
Workforce & Operations
Cleanroom Commissioning
Supporting environmental validation and qualification.
Manufacturing
We support aseptic manufacturing teams to optimise process flows, reduce waste, and meet regulatory expectations, without compromising safety. Our input includes:
Batch workflow design, including staging, reconciliation, and in-process checks
Line clearance walkthroughs and documentation alignment
Support with first fills, setup/hold time reviews, and cleanroom handovers
Practical troubleshooting for workflow gaps or delays
We draw on real operational experience to make your processes faster, safer, and easier to audit.
Facility Design
We prepare teams for MHRA inspections and internal audits with a calm, structured approach. Our support includes:
Full mock audits tailored to your site’s scope and risk areas
Live feedback during walkthroughs, plus a written report with RAG findings
Coaching staff on how to respond to inspectors confidently and clearly
CAPA suggestions based on real-world MHRA experience
We don’t just help you fix gaps, we help your team understand what good looks like.
Aseptic Preparation
We provide practical support to ensure your aseptic preparation processes are safe, compliant, and efficient. Our input includes:
Advice on setup, equipment checks, and critical step sequencing
Hold time risk assessments and validation strategy
Workflow improvements for media fills and cleanroom entries
Operator support on best practice aseptic technique
Whether you're running daily chemotherapy production or complex clinical trials, we help ensure every step stands up to MHRA scrutiny.
Quality Management
Our Quality Management support spans the full lifecycle of a robust QMS, from initial setup through to audit-ready maturity. We assist in designing and reviewing:
Quality Manuals with clear scope, authority, and document control strategy
Hierarchy maps that define the relationship between SOPs, policies, and work instructions
Deviation and change control workflows tailored to your team's structure and communication flow
Governance structures that embed quality at every level, including QRM, self-inspection, and CAPA oversight
Capacity planning models to ensure staffing, batch volumes, and documentation flow align with MHRA expectations
KPI frameworks that drive continuous improvement through meaningful quality metrics
All documentation is designed for daily operational use, not just compliance and informed by our direct experience in licensed manufacturing roles. Whether you're refreshing a legacy QMS or building from scratch, we provide practical, inspection-tested tools to keep your operation audit-ready and scalable.
Cleanroom Commissioning
We support teams through the complex process of bringing cleanrooms into GMP operation, including:
DQ, IQ, and OQ planning support
Environmental monitoring (EM) strategy and zoning reviews
Qualification and first fill planning aligned to Annex 1
Gowning assessments and visual inspection readiness
Review of commissioning reports and cleanroom supplier handover
Whether it’s a new build or refurbishment, we help translate specs into operational reality.
Workforce & Operations
We offer hands-on support in shaping the workforce and daily running of aseptic services, including:
Defining roles, banding, and escalation structures
Rota design for 7-day services or extended shifts
Coverage models and annual leave planning for critical roles
Building positive culture through structured meetings and communication
Operational readiness assessments before go-live
We’ve helped build departments from scratch and can help yours run smoothly from day one.
Document Support
We help organisations improve their document landscape, ensuring alignment with MHRA and GMP expectations, including:
Authoring clear, audit-ready SOPs, work instructions, and log templates
Reviewing and reformatting legacy documents for clarity and traceability
Structuring document hierarchies across Quality Manuals, policies, and procedures
Supporting controlled document lifecycle management (versioning, approval, and archive)
Embedding good documentation practices from Day One
Let’s Build Something That Works
From full aseptic start-ups to streamlining routine prep, WinnPharma supports organisations that want more than templates. We bring practical, proven systems that match MHRA expectations and real-world pressure.
Got a project in mind? Let's talk.
Audit Preparation
We support teams preparing for regulatory inspections by offering realistic and structured audit readiness services, including:
Mock inspections aligned with MHRA and internal standards
Document walkthroughs to identify gaps or outdated procedures
Staff coaching and practice Q&A for common audit lines of inquiry
Environment and documentation flow assessments from a GMP lens
Action plans to address findings with realistic timelines
Whether you’re inspection-ready or just starting out, we’ll help you strengthen confidence and control.
Training Packages
We create tailored training solutions that build capability and confidence across all levels of your team, including:
Designing role-based induction and annual refresher programmes
Creating visual and written content for SOP-based learning
Developing competency assessments and tracking tools
Building training matrices aligned with regulatory requirements
Supporting audit trails and records for inspection
Your team deserves training that actually prepares them for the job